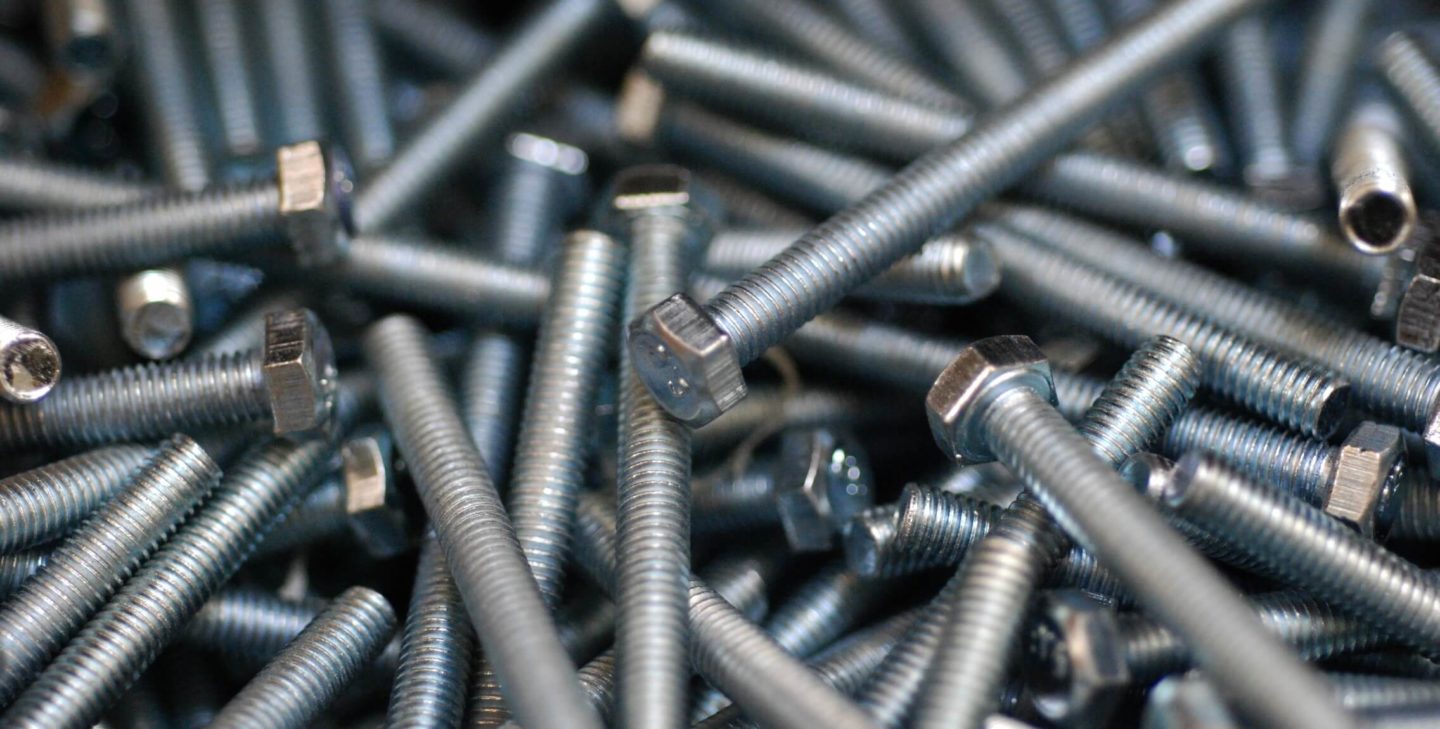
What Is Dip Spin?
Usually priced by the pound, in a dip-spin, bulk application coating process parts are dumped into a perforated basket and immersed into a coating. The basket is then raised from the vat and spun at a high RPM, which removes any excess coating with centrifugal force. The parts are cured and the process is repeated as needed depending on the coating recipe or thickness requirements.
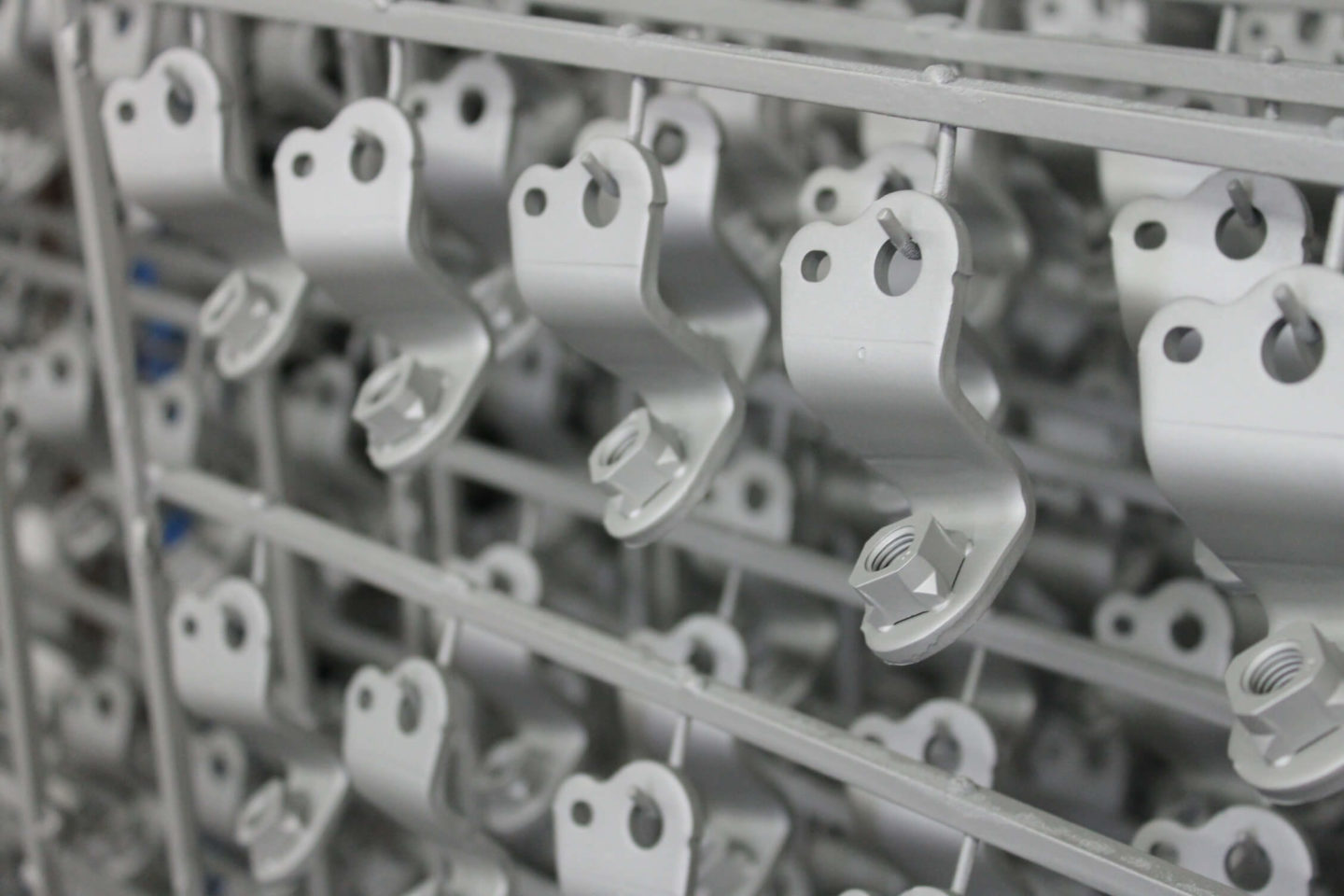
What Is Rack Spray?
Priced per piece, the DECC Company applies functional coatings almost exclusively via a rack-spray process. Whether it be on our electrostatic line, our hand spray line, or in our Research & Development department, almost every part we process is individually hung on a fixture, coated, cured on the fixture and then hand packed into customer dunnage.
Below you can find a white paper that is based on actual case studies and current market data.
Rack Spray 
Pros
- Less cost overall
- Less labor
- Faster Turn Around
- No need to Scrap
- No Need to Sort
- Direct Ship to End Customer
Cons
- Not suitable for small to mid-sized fasteners or hardware with numerous stamping geometries
Dip Spin
Pros
- Ideal solution for a vast majority of small to mid-size fasteners or hardware and for numerous metal stamping geometries
Cons
- Overall cost is affected when considering Cost of Poor Quality (COPQ)
- Bends and pockets can result in pooling of coating
- Thinner gauged metal can bend & distort in processing
- Geometries can get tangled
- Nearly flat parts can nest, causing voids or inconsistent coverage, or becoming fused together
- Cost of sorting & packing
- 20% Fallout requiring reworking or scrapping
The True Cost
In almost every case, dip-spin pricing is less expensive than a rack-spray price. However, this is true if you take the dip-spin pricing vs the rack-spray pricing at face value only. When taking into account the cost of poor quality (COPQ) of a dip-spin application for certain parts, rack-spray pricing could end up more advantageous in the long run.
Download Infographic PDF here.

Ship to Dip-Spin Coating
Ship to Rack-Spray Coating
The DECC Rack Spray Solution
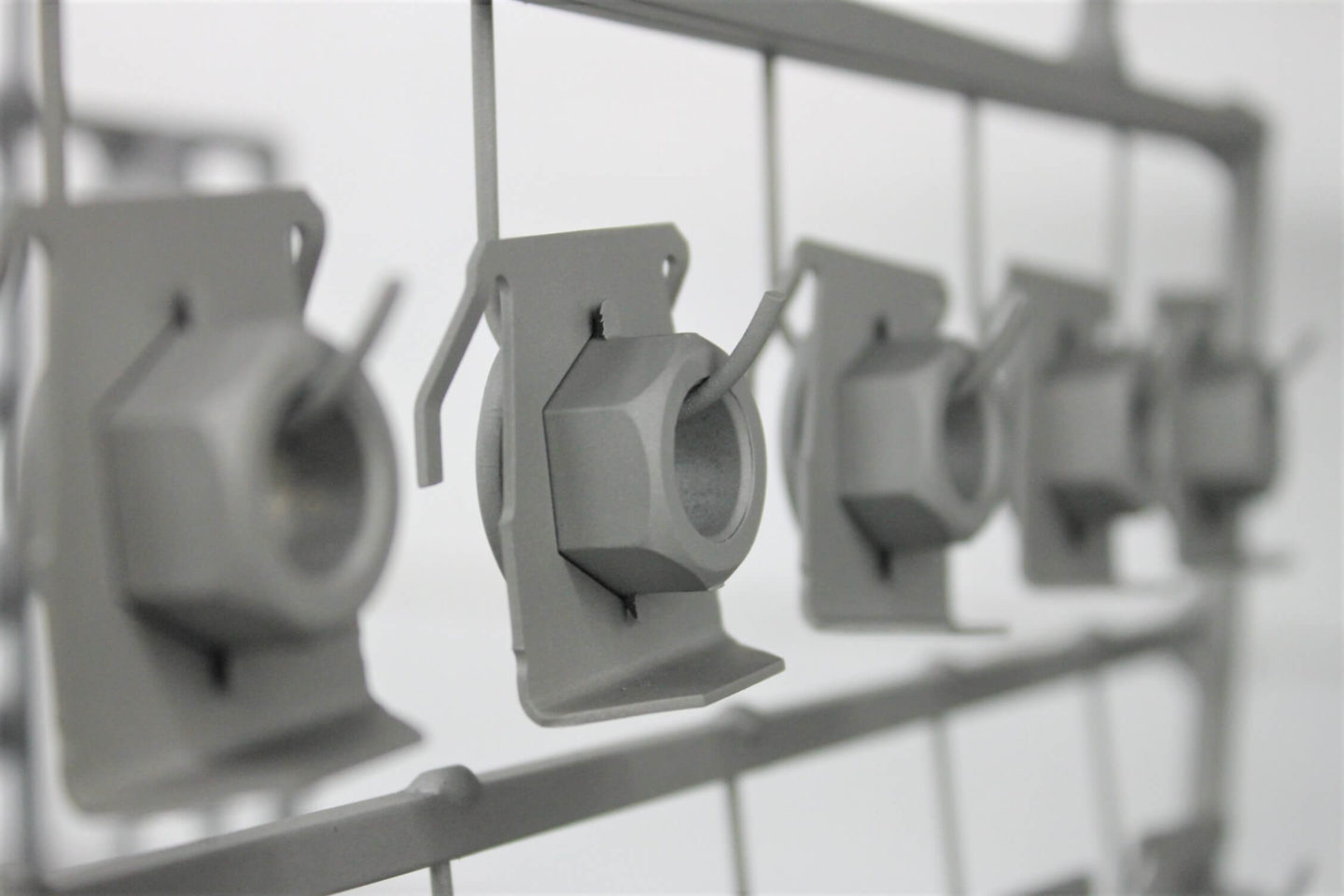
Less Waste
Until recently, even though a dip-spin application would not be ideal for some complex part geometries, it was the only effective way to ensure complete coverage on a component outside of a manual hand-spray, which would be too costly or not feasible for high-volume production. As a result, manufacturers would just have to succumb to the fact that they would need to sort, scrap and/or rework their product after the coating application.
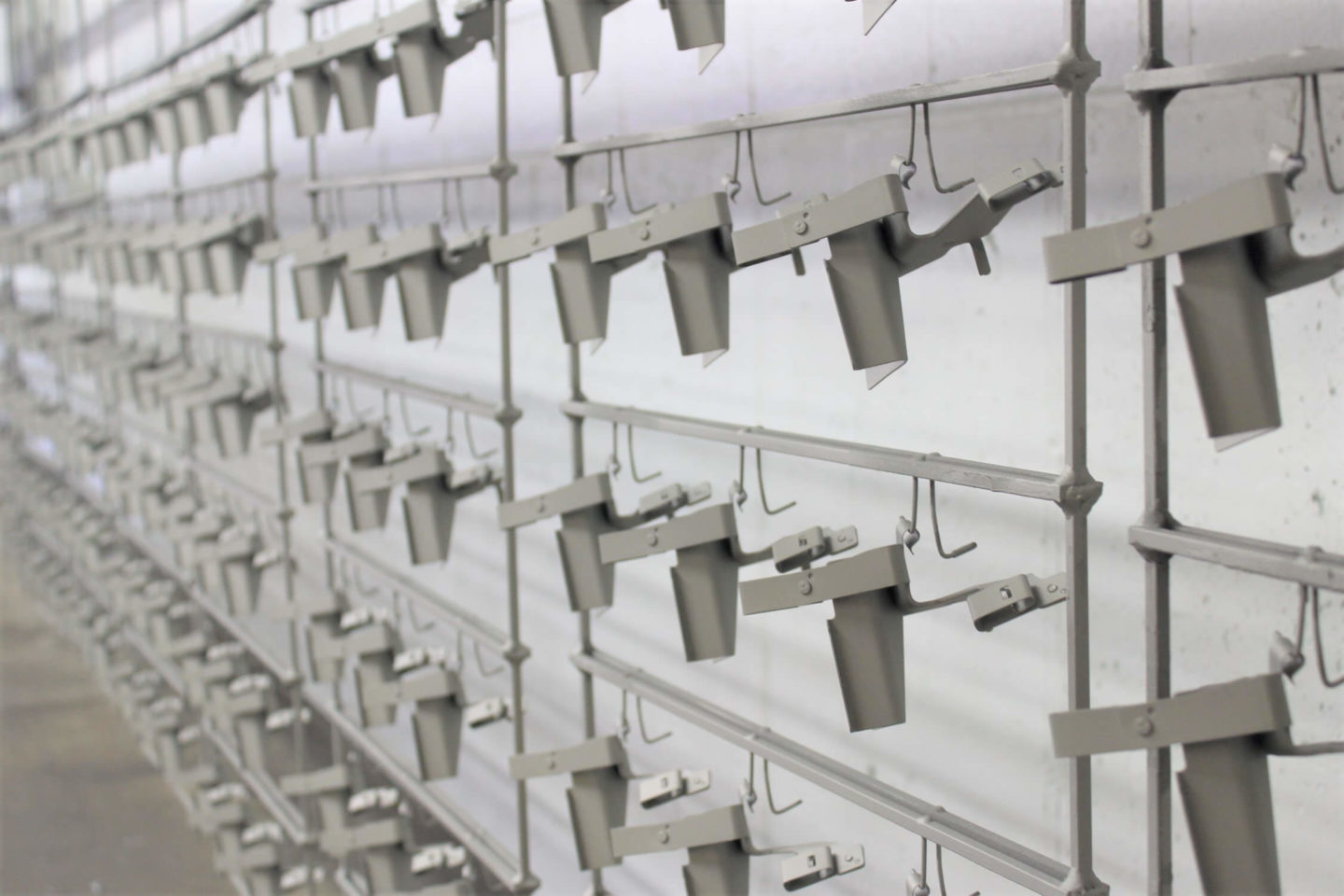
The Best Coverage
To combat this situation for current and potential customers with complex part geometries, DECC has installed two six-axis FANUC robots for touchup purposes on the back end of our electrostatic line. Utilizing this method, DECC is able to coat most of the part with our electrostatic guns and then obtain complete coverage with our robots, ensuring every nook, cranny, and crevice of a component is covered.
Dip-spin is the ideal solution for a vast majority of small to mid-size fasteners or hardware and for numerous metal stamping geometries. In these cases, it would not make sense to pursue a rack-spray application as the benefit would not outweigh the cost. Dip-spin coating has been the gold standard for these types of components and will continue to be in the future.
If you have any questions on what is best for you, let us know!