The DECC Company’s core competency is the rack-spray application of functional, high-performance coatings for the automotive industry, especially in high-volume programs. With quality focused process control and application methods, DECC is capable of adhering to a vast array of OEM coating specifications. As a coating applicator, DECC also has extensive experience solving unforeseen component problems through the application of functional automotive coatings.
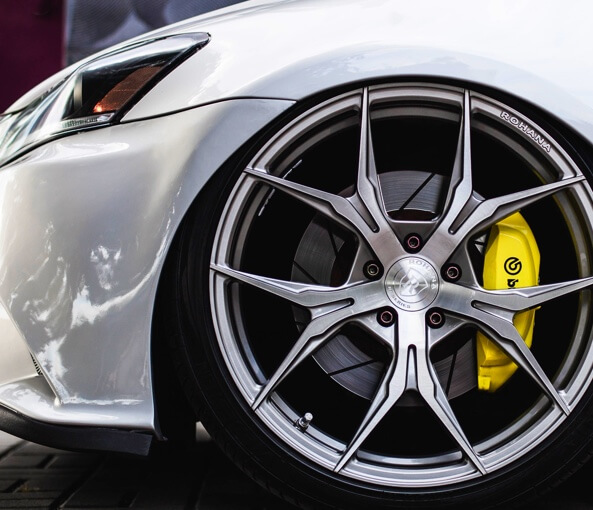
Typical Automotive Problems and their Coating Solutions
Road Noise
Creaking, Rattling, Buzzing, Humming:
DECC applies dry film lubrication and noise reduction coatings that deaden sound and enhance component performance
Corrosion Damage
Components rust or corrode due to environmental or chemical exposure:
DECC applies our corrosion protective coatings which have proven success on fittings, stampings, castings, and numerous other automotive components
High-Temperature Damage
Engine components and mating parts overheat and performance degrades:
DECC applies heat resistant coatings which are designed to deflect damaging heat from being absorbed by the part
Rubber to Metal Bonding Adhesives
Rubber doesn't stay attached to metallic surface on the suspension and engine-to-body mounts:
DECC applies rubber to metal bonding adhesives that allow for over-molding of rubber to a metal substrate
Protecting Your Components with Functional Automotive Coatings
Automobile OEM’s know that their customers demand quality and longevity out of their vehicles. To ensure this, car manufacturers turn to functional automotive coatings that enhance the performance and lifespan of critical car components. Almost every part in a car is connected to a coated component. From preventing corrosion to limiting UV damage, to reducing noise and more, functional automotive coatings keep your car performing better and longer.
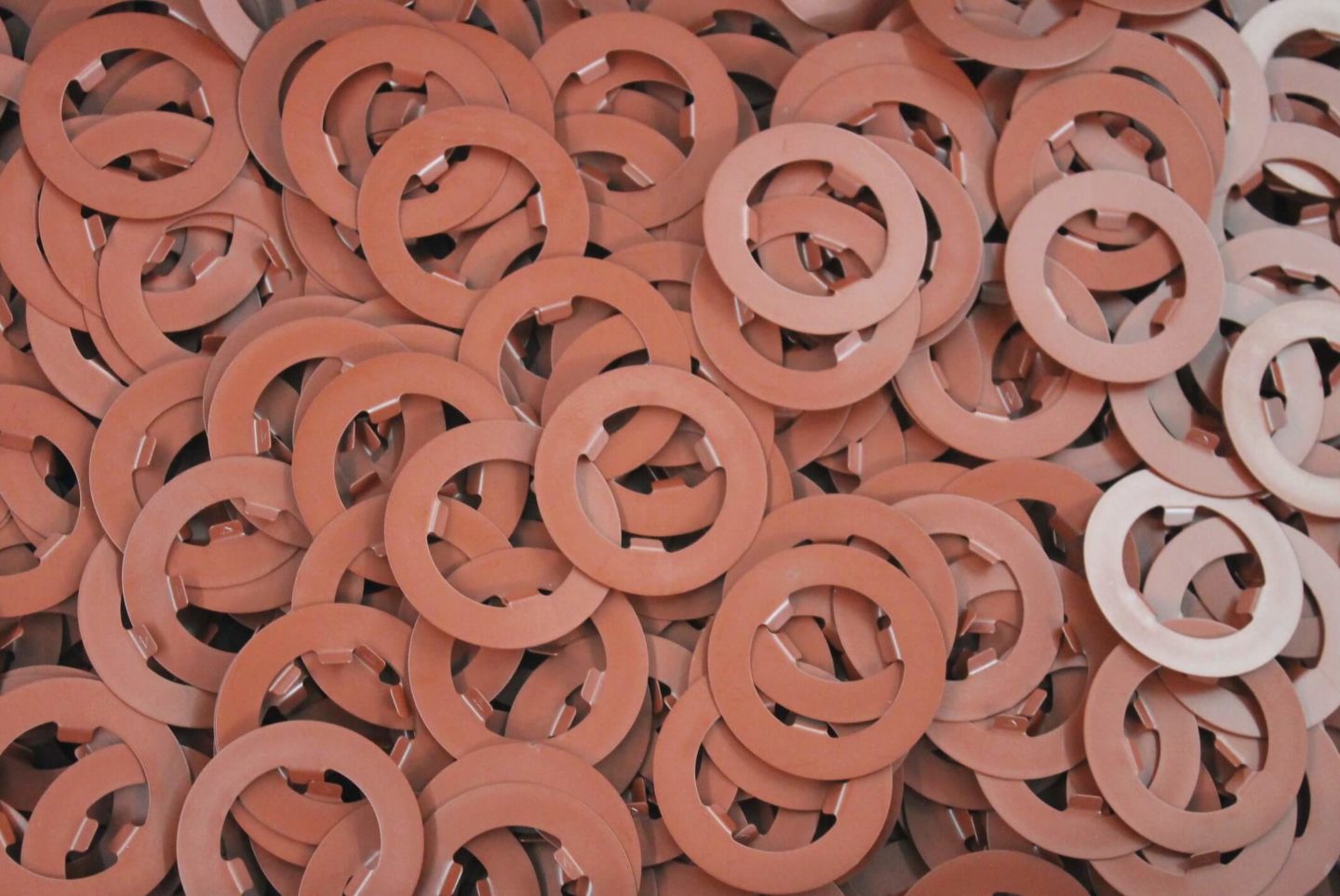
Examples of Commonly Coated Automotive Parts
Thrust Cage Bearings
Release coatings can be applied to thrust cage bearings that operate in the compressor of air conditioning units to ensure uninhibited starting after sitting idle for extended periods of time. DECC applies Whitford’s Xylan 1052 on these particular components.
Wheel Assembly Washers
Dry film lubricants are applied to enclosed transmission washers where traditional greases cannot be utilized, ultimately decreasing noise, increasing part performance and reducing harmful friction that contributes to premature component failure. DECC applies four different Xylan 1014 colors on such washers for not only functionality but for identification purposes at the point of assembly.
Brake Clips
Abrasion resistant coatings that also exhibit release properties are used on brake clips to eliminate squeaks and groans associated with braking and vibrations. DECC applies Henkel Bonderite S-FN 333 currently on brake clips. This coating, chosen by DECC in development, performed so well that the testing machine was shut off before any sign of coating failure.
Door Strikers
Durable, corrosion resistant zinc-flake coatings are applied to plated door strikers to provide an added layer of protection, not achievable by plating alone, for a component that is visible from the exterior of the vehicle and continually subjected to impact. Multiple coating systems from Magni are approved for automotive door strikers, including Magni 560, Magni 565 and Magni 510.
Steering Column Components
Graphite and molybdenum based dry film lubricants are ideal for components that actuate inside another as they allow for a transfer of coating to interacting parts, all the while performing in harsh chemical or atmospheric environments. Dow’s Molykote D-7409 is ideal for applications such as this.
Exhaust Gaskets
High-temperature resistant coatings are applied to exhaust gaskets to prevent fretting from part expansion and contraction during cycles of operation, as well as elevated continuous operating temperatures and vibration, ensuring an airtight seal, extended performance, and reduced maintenance. Cavero Coatings manufactures resin systems designed solely for this type of application.
Gas Filler Tubes
Corrosion resistant coatings, ultimately more durable than typical plating, are utilized on gas filler tubes for protection from the elements, as well as gasoline while standing up to frequent encounters with a gas pump nozzle. DECC currently applies a Magni top coat, B18, over drawn galvanized gas filler tubes for added corrosion protection.