In terms of functional coatings, there are numerous applications methods that are utilized in the industry.
Rack-spray, rack-spin, chain-on-edge, tumble-spray, dip-spin, and tilt-tumble are all methods for applying coating and each is unique in the way they achieve it.
Each one has their pros and cons depending on the coating required and, more importantly, the geometry of the component.
When requesting a quote from an applicator for your coating needs, make sure you are contacting a company that specializes in the coating application method that is most suited for your particular component.
Below are the functional coating application methods in the industry that are more “soft-touch” and which type of components are best suited for that particular method. Next week we will cover the bulk application side of things.
First and foremost, regardless of the geometry, parts requiring a smooth, cosmetic surface finish should be rack-sprayed, rack-spun, or coated on a chain-on-edge system.
Rack-Spray

Example parts suited for a rack-spray coating application. Many of these started off in dip-spin and came to DECC after quality issues presented themselves. Note: parts are not to scale.
DECC is almost an exclusively rack-spray coating company. This method involves hanging or placing a part on a fixture and then spraying the coating utilizing either electrostatic guns, HVLP guns, or a combination of both. Both types of guns could be either automated or used by a hand-spray technician.
Parts most suited for rack-spray are almost or completely flat components (like washers or snap rings as they nest in bulk applications), metal stampings with recessed pockets where coating could pool if bulk processed, components that can become tangled or distorted when bulk processed, heavy components, and anything that requires masking. Examples of some such parts are below.
Small fasteners, bolts, nuts, hardware, and tightly coiled springs are not very well suited for a rack-spray application. Components that require coating in areas that are not “in the line of sight,” such as hollow part geometries or parts with small or deep thru holes, are not well suited for a spray application either.
Rack-Spin
This is a relatively new application method…to North America, at least.
Rack-spin is similar to dip-spin except that no parts touch during processing. As its name suggests, components are racked to, or placed in, a fixture inside of a barrel. This barrel is then dipped into a vat of coating, completely submerging the parts.
The barrel is then lifted out of the coating, or the coating is drained from the vat, and the barrel is spun at a high RPM. Centrifugal force spins off any excess coating. The entire rack is then placed on a conveyor, cured, and if required, the process is continued until the necessary coating thickness is achieved.
This type of application method is ideal for oversized and very complex geometries, such as heavy metal assemblies with multiple welded assemblies or large frame components with hollow design features, where complete coating coverage is necessary.
The same limitations that are present for rack-spray parts on small fasteners, bolts, nuts, hardware, and tightly coiled springs would prohibit them from this application as well. Additionally, small to medium size metal stampings that are suited for rack-spray, but not dip-spin, would also not be an ideal fit for this coating method because a high-volume rack-spin price would be considerably higher when compared to a high-volume rack-spray application on the same component due to thru-put limitations.
For an overview of rack-spin coating and to gain an idea of parts suited for such a process, watch this informational video from Magni Coatings below.
Chain-on-Edge
Chain-on-edge coating systems start with placing a component on a spindle fixture of some kind. These spindles then move along a guided chain thru the coating process.
When they reach the point of coating application in the system, the spindles are engaged and the part then begins rotating as it passes in front of the spray gun, ensuring a consistent film build on the entirety of the part. Most systems have in-line curing steps after the part is coated. Below is a video of DECC’s chain-on-edge system that was utilized for coating projectiles for the military.
Based on the above description and accompanying video, it is easy to see that there are a limited number of part geometries that are suited for this application method.
Cylindrical components are really the only type of geometry that works on a chain-on-edge system, such as armatures or projectiles. Some systems can coat both the OD and ID of a component if required. Larger bolts can also be a good fit for this type of system if fixtured properly.
However, outside of the above, there really aren’t many other types of components that fit this coating application method…but it should be noted that this is an extremely effective and efficient method of coating the ones that do.
For parts requiring a “soft touch” process and needing a consistent, smooth surface finish, the above application methods are your path to success depending on part geometry, which was hopefully explained well enough to make a more educated choice.
If not, please feel free to contact us and if we cannot provide a solution, we will help you find someone who can.
Next week will be part two on this topic and will elaborate on the various bulk method coating application methods in the industry.
Related Articles
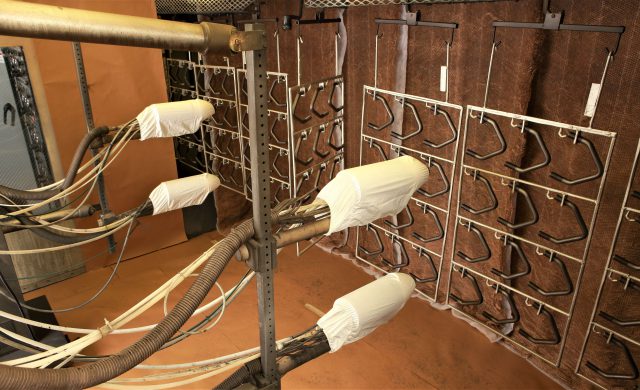
How to Choose the Right Coating Application Method: Part One
In terms of functional coatings, there are numerous applications methods that are utilized...
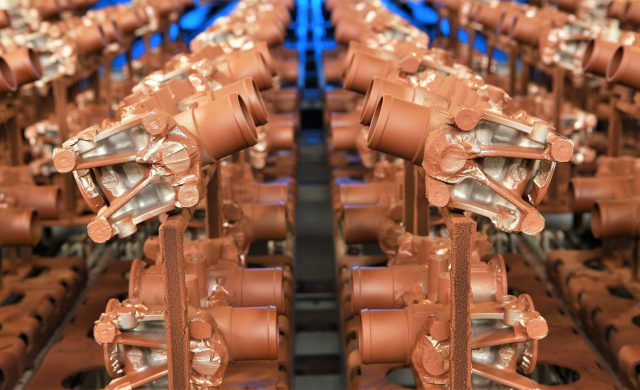
Corrosion Protection: Sacrificial vs Barrier Coatings
Corrosion is one of the leading causes of component failure across all industries....
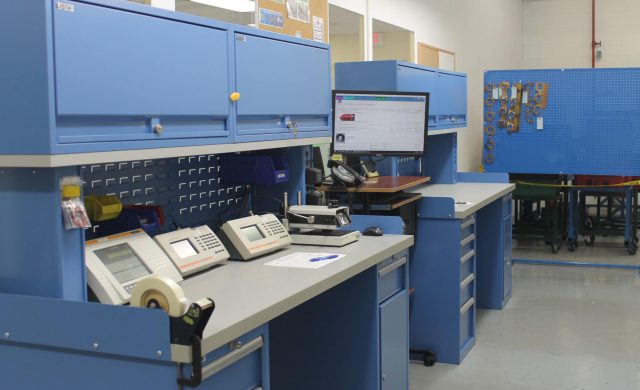
Dyne Testing for Surface Cleanliness
What is Dyne testing? Our last blog detailed the various methods of which to prep...