A coating only performs to the level of the surface of which it is applied.
In other words, if the surface of a component is not adequately prepped before the application of a coating, that coating will not perform. This goes for not only the high-performance, functional coatings that DECC applies, but all coatings.
There are three main types of surface preparation that can be performed prior to applying a coating.
Thermal prep
- Placing parts into an oven at a predetermined temperature
- Temperature is determined based on the final coating used and the substrate being baked. Prebake temp must be above the final cure temperature of the coating by at least 50°F. This ensures that anything embedded in the substrate will be removed/released prior to the curing step after coating and not during the curing step. However, the substrate must be able to withstand the prebake temperature.
- Prebaking will burn off oils and grease, but the dirt particulate embedded in the oil may still be present. That is where a mechanical removal may have to be introduced to remove contaminants completely.
Mechanical prep
- Blast
- Introduces abrasive particles in a compressed air stream, impacting the surface of the part. This creates microscopic peaks and valleys, which is an ideal surface profile for which coating can bond.
- There is a wide range of grit sizes and materials that can be used (DECC uses 70 grit aluminum oxide). Typically the lower the number the grit sizes, the more aggressive the profile that will be left on the part surface…the higher the number, the less aggressive.
- Parts can be bulk tumbled or individually hand blasted – it is all dependent on part geometry, substrate, and size.
Hand blast using aluminum oxide
- Steel shot
- Similar to blasting, but with a different delivery method. Steel shot is slung at the parts, peening the surface. The steel shot has a spherical shape, similar to a small BB.
- This is typically used to remove baked-on contaminants from the surface of the part, but it will not aggressively etch the surface. It will peen the surface and smooth over sharp edges.
- A wide range of steel shot can be chosen to change surface profile.
Chemical prep
- This is typically a dip process where the parts are immersed in a chemical or detergent cleaner or degreaser but can be done using spray nozzles directed at racked parts on fixtures.
- Effectiveness can be amplified with the addition of ultrasonic waves to the bath if the immersion process is being utilized.
- Cleanliness of the surface can be measured on a dyne scale, where the higher the dyne score, the cleaner the surface. The cleaner the surface, the better the adhesion of the coating to the substrate.
- Another surface treatment that is a chemical prep is phosphating, in which a thin layer of microcrystalline zinc is added to the surface of the part. The solution reacts with the base metal and binds it to the surface. This is usually done when added corrosion protection is needed or a mechanical etch is too aggressive for the part. The zinc layer gives a rougher profile to which the coating can bond as opposed to a standard alkaline wash. Standalone phosphating does not offer a great deal of corrosion protection, but it will provide some – it all depends on the type of phosphate layer being added.
The above are processes that the DECC Company can provide internally and are just a few of the potential options throughout the coating industry. Each process is selected based on part material, geometry, and coating system applied.
As mentioned, one of the leading causes of coating failure is an inadequate surface prep. If you have questions or need help troubleshooting a coating failure with your current source, we can help you figure out a solution.
Contact UsRelated Articles
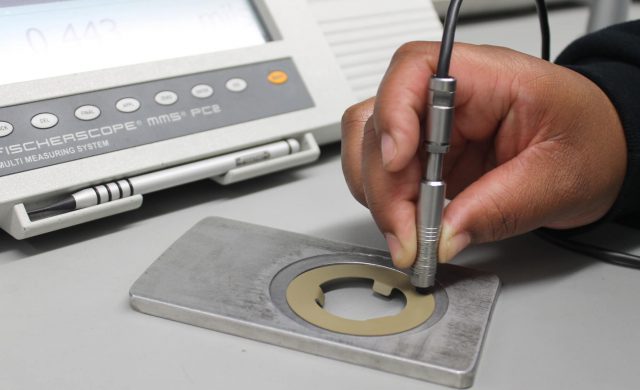
How to Center Your Process in a Coating Application (Here’s a Hint: You Can’t)
In every quality position, in every market, the goal is always the same:...
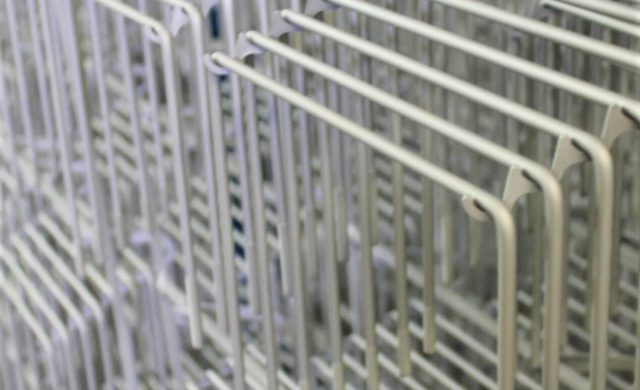
How a Rack-Spray Process Audits Your Parts
Utilizing a rack-spray coating application for your components as opposed to a dip-spin method has...
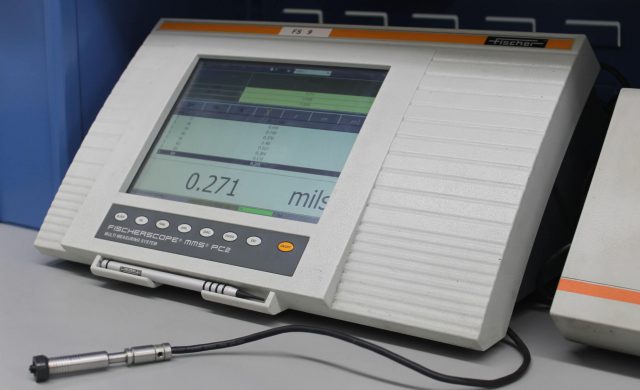
The Three C’s: Coverage, Cure & Cross Hatch
Will the coating pass this test or that? Will it reach this many...