Will the coating pass this test or that?
Will it reach this many hours in salt spray?
Can it withstand this temperature?
Customers often ask us technical performance questions about the coatings DECC applies. Depending on the coating, our answer is usually some variation of “it should…”
This may seem like a cop out. Why won’t we stand behind or guarantee a coating’s performance? As DECC is only a coating applicator, we do not manufacture the coating. Magni, Doerken, Dow, Henkel, etc, design and produce their coatings to meet certain performance characteristics. They tell us what their coatings will do. As long as DECC applies the coatings per the manufacturer’s process recipe, they should exhibit all the performance attributes of which they were designed.
So how do we ensure that the coatings are applied correctly? With the three C’s: coverage, cure and cross hatch.
Coverage – a coating will not perform if there is not complete coverage of all functional areas of a component. DECC ensures coverage two ways: visual inspection and a measurement of the coating’s thickness. Visually, the substrate must not be visible thru the coating. Thickness is measured using a Fischerscope or a beta backscatter depending on the substrate. The thickness must be at a minimum of what is required per the coating’s product data sheet.
Cure – we talked about the importance of cure and full film properties in a previous blog post. If a coating is not fully cured, it will not exhibit all of its intended performance characteristics. To check if a coating is properly cured, we will wipe the coated surface a designated number of times with a solvent, such as MEK. Once complete, there should be no transfer of the coating to the wipe.

An X cut is made on a component prior to the quality tape being applied to check adhesion
Cross Hatch – we also talked about the need for a quality surface prep method in a previous post, which is essential for proper coating adhesion. If the coating doesn’t stick to the substrate, it will fail. To check for proper adhesion, we perform a cross hatch test. This entails basically cutting the coating in a pattern or grid per the applicable coating specification. Once all the cuts are made, a piece of tape is placed over the top of the cross hatch and then slowly peeled off. If the coating has been applied correctly, there should be little to no coating on the tape.
If we have done our job correctly, the coating should pass the above three tests. And if it does, it should display the performance characteristics for which it was designed. However, as we like to say, each application is different and each environment a component operates in is unique…the best way to verify performance is to test a part after it is coated.
If so, be sure to contact us. We can apply a variety of coatings to ensure you have the right solution for your particular challenge.
Contact UsRelated Articles
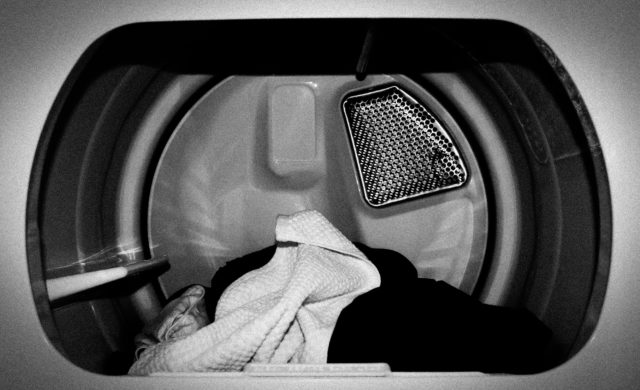
Reduce Plastic Sticking with Dryer Panel Coatings
DECC SOLVES PROBLEM OF PLASTIC STICKING TO DRYER PANELS
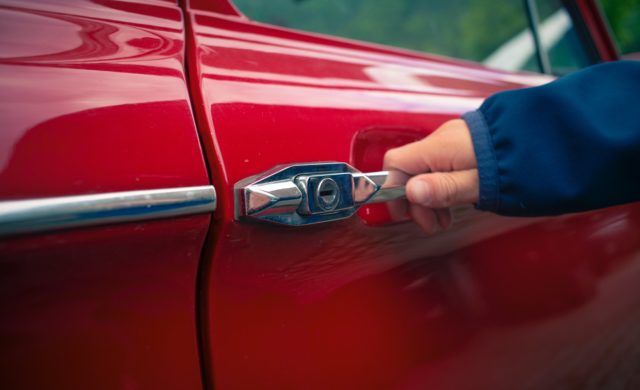
Coatings for a Quiet Ride
As cars have gotten quieter and quieter over the years, auto makers have...
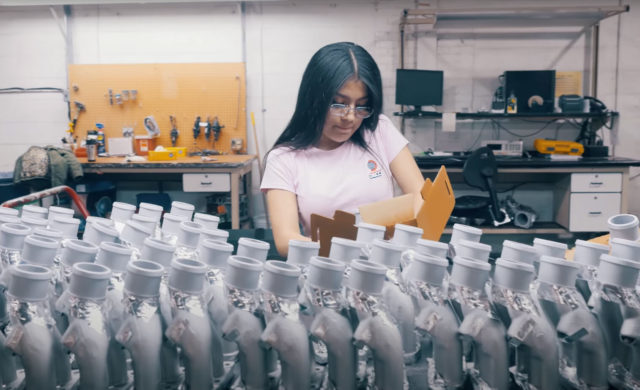
Dip Spin vs. Rack Spray – Why Not Both?
When it comes to the application of liquid-based functional coatings, there are two...