Galling is a form of adhesive wear caused by two metal surfaces that are in relative motion and under load. Without proper lubrication, this can cause a high-stress condition where surface protrusions of the mating components can build over time, significantly impacting part performance. In severe instances, complete seizure of interfacing metal parts can occur.
Galling was the exact problem a local automotive parts manufacturer was facing in regards to a safety-related assembly they produced.
The assembly in question was the mechanism that prevents shifting a car into gear without first engaging the brake. The assembly included a small metal armature that would actuate inside of a metal housing. There was no lubrication between the components and they began to seize well before the 900,000 required cycles for product validation were achieved.
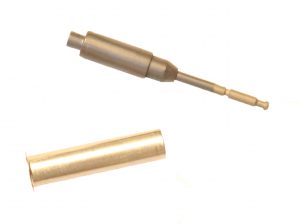
The two mating components, the armature with a dry-film lubricant applied
The company contacted DECC for a solution. Based on our knowledge of dry-film lubricants and how they are designed to function in different environments, we offered two options.
One of the coatings we applied was Molykote D-7409. This dry-film lubricant is ideal for metal to metal combinations with slow to moderately fast movements in medium to high load capacities. This coating also contains molydisulfide, a solid lubricant capable of transferring to mating components, ultimately resulting in two lubricious surfaces.
The second coating we applied was Henkel’s Bonderite S-FN 333, most commonly referred to by its old trade name Emralon 333. This dry-film lubricant is not just PTFE, but a blend of fluorocarbons. As a result, this particular coating allows for a reduced coefficient of friction while providing additional abrasion resistance not typical of a pure PTFE coating.
Once applied to sample parts, both were put on rapid cycle testing for evaluation…and both performed exceptionally.
The D-7409 exceeded 1.8 million cycles before failure, or more than double the initial requirement.
However, the Emralon 333 lasted well over 2 million cycles before the testing machine was shut off and the part had yet to fail.
The customer felt each of the coatings applied were a success. However, given that both coatings were relatively priced comparatively, they chose to move forward with Henkel product.
It should be noted that there have been instances where the D-7409 has outperformed the Emralon 333. This is just another example of why DECC will typically recommend multiple coatings for testing as each one performs differently depending on the unique application.
If you are in need of a solution to a part performance problem, contact DECC today. As we are not a coating manufacturer, we consider ourselves “coating agnostic” and can offer a variety of different options for your challenge.