In a previous blog post, we talked about solving essentially the same performance issue with two different coating types. This happens frequently and sometimes it involves using not only different coatings, but coatings from completely different suppliers.
As a privately held coating applicator not owned by a coating manufacturer, DECC can approach solving customer’s problems from a dynamic position of not being tied to any single coating or coating manufacturer.
Sometimes this involves something as relatively simple as applying a coating that is called out on a specification for a customer.
For instance, a relatively common specification on prints for General Motors is GMW3359.
There are numerous coating recipes that, when applied correctly, meet this specification. DECC applies two of them – Doerken’s Delta-Protekt® KL 100 & Delta-Seal® GZ Silver and Magni’s 565 recipe.
Depending on a variety of factors, we may suggest one or the other…it really depends on which recipe allows us to offer our customer the most competitive price while maintaining a high level of quality. But the main takeaway is we have that option and can offer that choice to our customer.
Our ability to offer a variety of coating solutions really shines in the instances a customer approaches us with a part performance challenge for a component that is already in production.
Typically, our customer is in a “crisis mode” when this happens – a squeak has been found, a part is failing prematurely, a component is not functioning properly, etc. Because of this, the need for a solution is required as soon as possible.
When those challenges are presented to DECC, we usually take the buck shot approach – apply a few different coating resins we believe can solve the problem to a group of samples so they can all be tested and evaluated at the same time. If we are given three samples to coat, we may put on three different coatings from three different suppliers.
If a dry film lubricant is needed and there are no restrictions due to the substrate material, we may apply Whitford’s Xylan 1010, Henkel’s Bonderite S-FN 333 (formerly Emralon 333) or Molykote® D-708 and let the performance testing be the judge. Each of the aforementioned coatings could all solve the issue, but they also all come at different price points. This allows the customer the ability to choose which coating’s performance they feel can justify the price required to solve the problem.
The only time DECC deviates from the above practice is if an opportunity is brought to us by one of our suppliers – we will offer only that supplier’s coating as an application choice.
If you are experiencing a part performance issue and want a variety of solutions to try, contact DECC today.
Related Articles
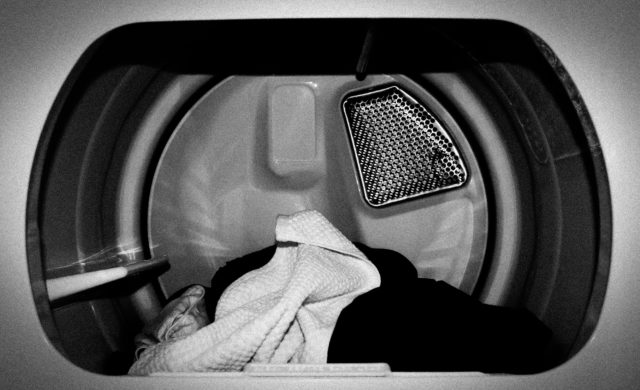
Reduce Plastic Sticking with Dryer Panel Coatings
DECC SOLVES PROBLEM OF PLASTIC STICKING TO DRYER PANELS
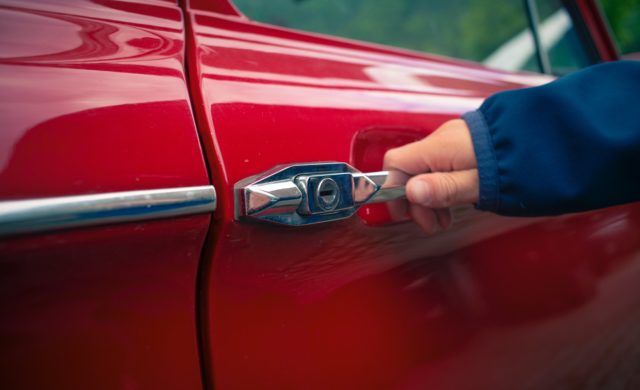
Coatings for a Quiet Ride
As cars have gotten quieter and quieter over the years, auto makers have...
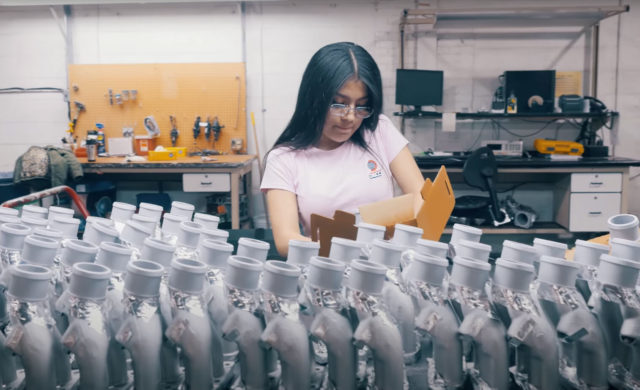
Dip Spin vs. Rack Spray – Why Not Both?
When it comes to the application of liquid-based functional coatings, there are two...