When it comes to the application of liquid-based functional coatings, there are two primary methods of application in the industry: dip-spin and rack-spray.
Dip-spin and rack-spray both have their pros and cons. And really, the “correct” choice has less to do with the process and more to do with the component. Based on the component’s geometry, one process might be better than the other—and at DECC, we’ll always recommend the right approach to our customers.
But what if you want the pros of both— high quality finish that also covers every little nook and cranny? For that, we do provide the option of utilizing both dip-spin and rack-spray.
Before that, let’s look at both processes in individual detail.
Rack-Spray
The rack-spray method involves hanging or placing a part on a fixture and then spraying the coating utilizing either electrostatic guns, HVLP guns, or a combination of both. Parts most suited for rack-spray are flat or nearly flat components (like washers which can stick together in bulk applications, metal stampings with recessed pockets where coating could pool if bulk processed, components that can become tangled or distorted when bulk processed (like snap rings or wire forms), heavy components, and anything that requires masking.
The Pro: A nice, cosmetic finish
The Con: Only covers surfaces reachable by the spray
Dip-Spin
Dip-spin works kind of like a washing machine—only we’re using coating instead of water. Usually priced by the pound, in a dip-spin, bulk application coating process parts are dumped into a perforated basket and immersed into a coating. The basket is then raised from the vat and spun at a high RPM, which removes any excess coating with centrifugal force. The parts are then cured, and the process is repeated as needed depending on the coating recipe or thickness requirements.
The Pro: Coverage over every exterior surface
The Con: A rougher finish
—
Important Note: In almost every case, dip-spin pricing is less expensive than a rack-spray price. However, this is true if you take the dip-spin pricing vs the rack-spray pricing at face value only. When taking into account the cost of poor quality (COPQ) of a dip-spin application for certain parts, rack-spray pricing could end up more advantageous in the long run.
The Best of Both
There are certain cases where a component would benefit from both rack-spray and dip-spin processes—giving the component full coverage on every surface, no matter how complex its geometry. Some may see this as overkill – and on most products, it probably would be – but certain products, especially premium products, could benefit from this double process.
At DECC, we’ve recommended both dip-spin and rack-spray processes more than a few times with amazing results. And as far as we know, we’re the only company that provides this approach at this time.
If you need input as to which coating application would be the best fit for your component – dip-spin, rack-spray, both processes put together, or an approach not covered in this article – contact us today.
Contact UsRelated Articles
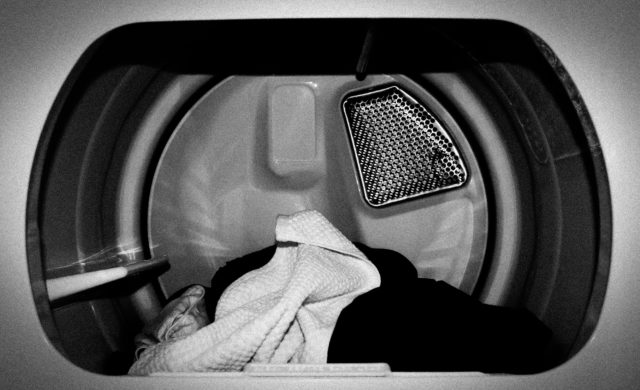
Reduce Plastic Sticking with Dryer Panel Coatings
DECC SOLVES PROBLEM OF PLASTIC STICKING TO DRYER PANELS
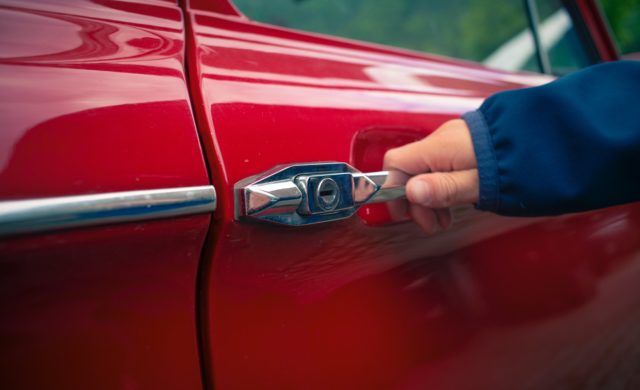
Coatings for a Quiet Ride
As cars have gotten quieter and quieter over the years, auto makers have...
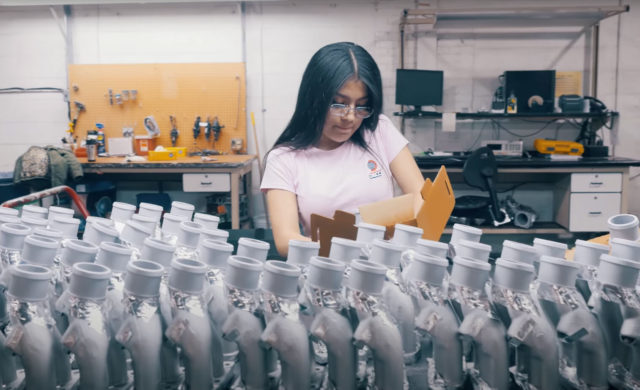
High-Volume Orders, Small-Volume Orders, and How Changeover Impacts Cost Savings
When a customer asks our team, “How much will this coating application cost?”...