As cars have gotten quieter and quieter over the years, auto makers have felt the pressure to eliminate NVH (Noise, vibration, and harshness) and BSR (buzz, squeak, and rattle) completely.
These issues have been rated as one of the primary quality issues for auto makers. Even the slightest nuisance can be a deal breaker for consumers, and that’s where PTFE coatings – also known as dry film lubrication – can offer a solution for a wide variety of components.
After nearly 60 years of working in the dry film lubrication industry, our DECC team has an immense level of understanding and historical data. We have evidence around what works best for each component, setting us apart from other suppliers with less experience. Backed by this experience, we can become your trusted partner – not just a transactional supplier – advising and delivering a repeatable result.
First and foremost, what are PTFE coatings?
PTFE (Polytetrafluoroethylene) is a fluoropolymer that provides a low coefficient of friction that prevents the scoring, galling, or sticking of mating components, which can ultimately eliminate squeaks and vibration. Some PTFE coatings, such as Henkel’s Bonderite S-FN 310A & Bonderite S-OT 310B, have lower curing temperatures and can be applied to plastic, silicone or rubber components.
PTFE coatings have a number of properties that make it useful to many industries. PTFE coatings are resistant to corrosive chemicals, provides good insulation from electricity, doesn’t absorb water, can withstand extremes of heat and cold, resists UV rays, and creates little friction. Many industrial PTFE coatings can withstand temperatures as low as -250ºF without loss of physical properties and can operate continuously at temperatures up to 260°C/500°F.
A PTFE coating’s unique makeup is what provides it with the non-stick, non-friction, and dielectric properties that make it useful in so many applications. PTFE coating is a fluorocarbon solid, meaning that it has a high molecular weight made up solely of carbon and fluorine. This make up makes it resistant to water, gives it a low friction co-efficient, and makes its other useful properties possible.
Where can PTFE coatings be applied?
PTFE coatings can be applied on – but not limited to – these items:
• Latches
• Brackets
• D-loops
• Care door strikers
• Steering column
How PTFE Coatings are Applied
PTFE comes in two basic forms, namely a “powder” and a “liquid”, and each has distinct methods of application. For our typical application, we will rack your part and spray it with electrostatic bells using liquid as this has excellent flow characteristics. The powder option is excellent as well, as it can be applied much thicker if the application involves high wear areas. The last step after either of these applications involves curing the PTFE-coated parts at high temperatures.
Uses of PTFE Coatings
Polytetrafluoroethylene is used as a non-stick coating for pans and other cookware used in food production. It is non-reactive, partly because of the strength of carbon-fluorine bonds and so it is often used in containers and pipework for reactive and corrosive chemicals. Where used as a lubricant PTFE reduces friction, wear, and energy consumption of machinery. It is commonly used in surgery at hospitals as well.
PTFE coating services are also frequently used to coat the inside of fuel and hydraulic lines. Because fluids may flow slowly in colder temperatures and higher altitudes, PTFE coating’s low-friction coefficient makes it helpful in ensuring these substances continue to flow as needed.
With regard to industrial applications, PTFE coating’s low friction is helpful in applications where parts may slide against one another, such as gears, slide plates, etc. A PTFE coating performs far better than other coatings, such as nylon in these applications. If the application is a break clip, sometimes a graphite is added because of the intense pressure that is applied.
While PTFE coating services may not be appropriate for every project, for many applications in a wide variety of fields, it’s the No. 1 choice for a non-stick, water resistant, dielectric coating. With our help, your company can determine whether it’s the right coating for your materials.
If you are looking for coating information and solutions, contact DECC to see how we can help.
Contact Us
PTFE, coatings provide protection against water, corrosion, friction, and more. A variety of industries have come to view PTFE as the go-to coating for thousands of applications.
Contact UsRelated Articles
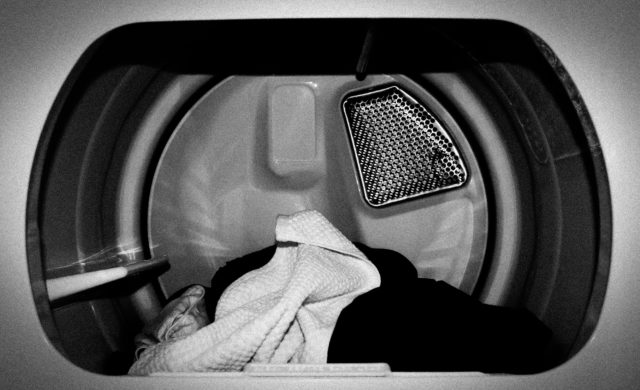
Reduce Plastic Sticking with Dryer Panel Coatings
DECC SOLVES PROBLEM OF PLASTIC STICKING TO DRYER PANELS
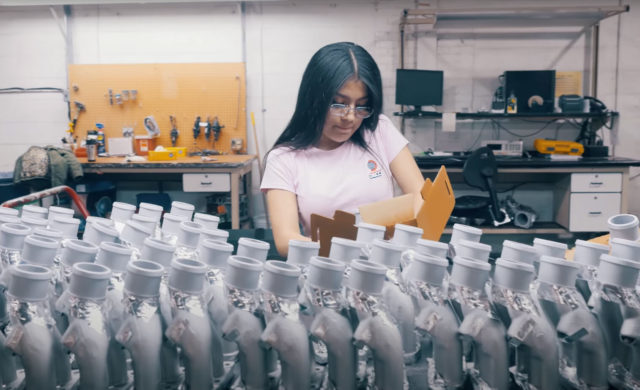
Dip Spin vs. Rack Spray – Why Not Both?
When it comes to the application of liquid-based functional coatings, there are two...
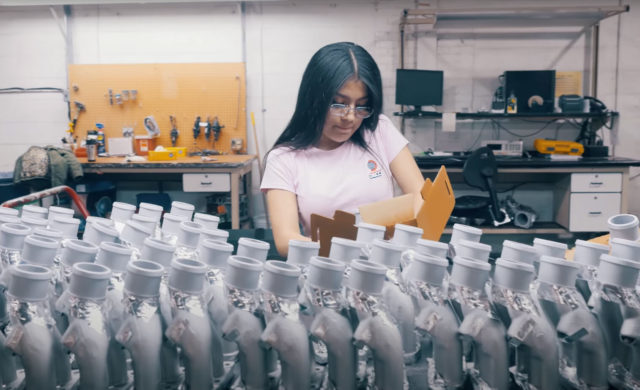
High-Volume Orders, Small-Volume Orders, and How Changeover Impacts Cost Savings
When a customer asks our team, “How much will this coating application cost?”...