We have posted numerous times about the advantages of a rack-spray finish compared to a dip-spin finish. In the vast majority of cases, DECC would prefer to apply coating via our electrostatic or hand spray lines.
However, as is the case with dip-spin, there are certain types of part geometries and substrates that are well suited for our tumble spray lines.
What is Tumble Spray?
Tumble spray, just like dip-spin, is a bulk coating application method and is a very economical choice in terms of pricing. Tumble spray components are priced at a fraction of the cost of rack-spray. However, that is where their similarities end.
Tumble spray involves placing components in a specially designed, hexagonal shaped unit. A controlled spray of atomized coating is then applied to parts as the unit rotates. The hexagon design of the unit is important as the components are flipped and rotated more than a simple cylindrical unit could. Once the coating is applied, parts are loaded in baskets and baked in a batch oven.
What Types of Parts Are Suited for Tumble Spray?
There are a variety of component and substrate types that can be coated via a tumble spray application.
Plastic, silicon, glass-filled nylon, and rubber parts are very well suited to be coated in a tumble spray unit. Typically, these parts are coated with a PTFE based coating for non-stick release, lubrication or chemical resistance.
Examples of such parts are O-rings, seals (large and small), gaskets, bumper bolts, and grommets, just to name a few.
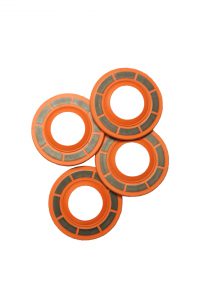
A silicon seal with a low-cure PTFE coating applied via the tumble spray method
Metal substrates, depending on their geometry and the type of coating required, can be coated in a tumble unit as well. Typically, dry-film lubricants are an ideal coating for a tumble application, most notably those rich in molydisulfide or graphite. These coatings are designed to transfer to mating parts after cure so they are exceptionally suited for an application method where components are constantly rubbing together before the coating is cured.
Examples of such parts would be tightly coiled springs, extremely small castings, trim clips, bushings, hinges, latch components, etc.
Regardless of the substrate, typically the geometries of these types of parts do not allow for them to be hung on a fixture.
Limitations of Tumble Spray
No coating application method is perfect as each one has certain limitations. In terms of tumble spray, certain types of coatings do not perform well in the tumble unit. As with dip-spin, completely flat components (like washers) can be problematic as there is the potential for them to stick together. Lastly, the surface finish of the part is not as uniform as a rack-spray finish because of the very nature of a bulk application.
Is Tumble Spray Right for My Component?
As we always say, the coating application method is really determined by the part substrate, part geometry, and the part performance requirement. Do you have a small plastic or rubber part, maybe an O-ring, which requires a PTFE coating? Then yes, our tumble spray could be an option. Do you have a small fastener or screw that requires a zinc-flake corrosion resistant coating? Then you would probably want to go the dip-spin route. Do you have a metal stamping that is relatively large and has a complex geometry? Then rack-spray would be the way to go.
If you need help determining which coating method is the right fit for your component, contact us today. Even if we aren’t the option, we will help you find someone who is.
Related Articles
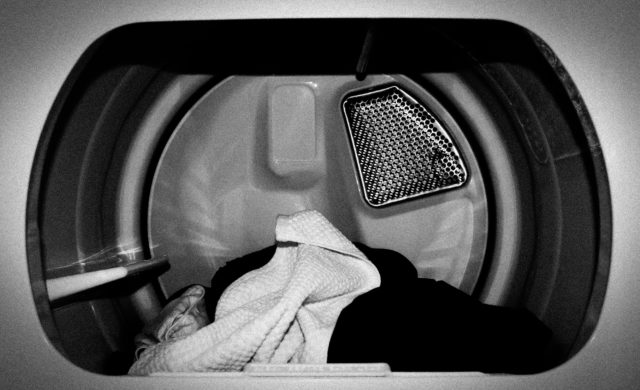
Reduce Plastic Sticking with Dryer Panel Coatings
DECC SOLVES PROBLEM OF PLASTIC STICKING TO DRYER PANELS
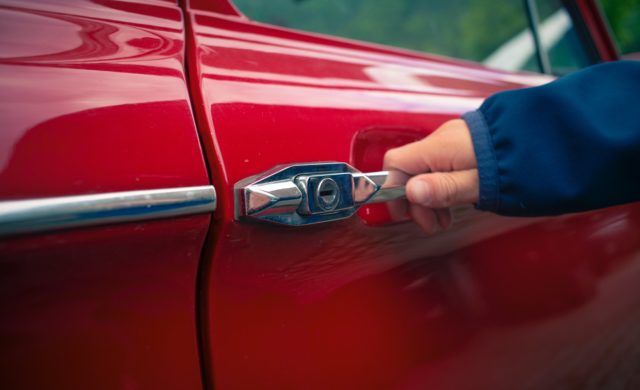
Coatings for a Quiet Ride
As cars have gotten quieter and quieter over the years, auto makers have...
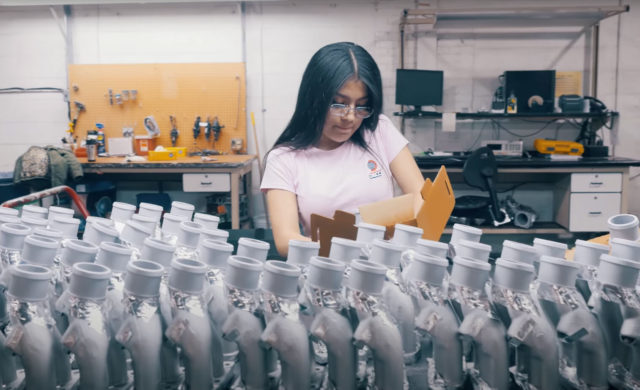
Dip Spin vs. Rack Spray – Why Not Both?
When it comes to the application of liquid-based functional coatings, there are two...