Simply put: there are part geometries that lend themselves to a dip-spin coating process and those that do not.
In fact, even though DECC is a rack-spray facility, we will be the first to direct a customer to a dip-spin competitor when asked to quote a part that is suited for such an application. A rack-spray process can be two to three times more costly than a bulk process and, when it makes sense, we want our customers to take advantage of such pricing.
However, for part geometries that are not suited for dip-spin, quality and delivery issues quickly negate any “savings” when the true cost of processing is evaluated.
After taking into account all the costs associated with sorting, rework, scrapping, and extra shipping, a rack-spray piece price is typically more advantageous.
Check out the infographic below to see what a side by side cost comparison looks like when a part not suited for dip-spin is coated in a bulk application.

Rack Spray vs Dip Spin Infographic
Also, if you are experiencing quality issues with a current production part and would like to do a side by side cost analysis with your own true costs, download our Dip-Spin vs Rack-Spray Cost Analysis template here.
If you would like DECC to quote a current or future production program with a rack-spray application, contact us today.
Related Articles
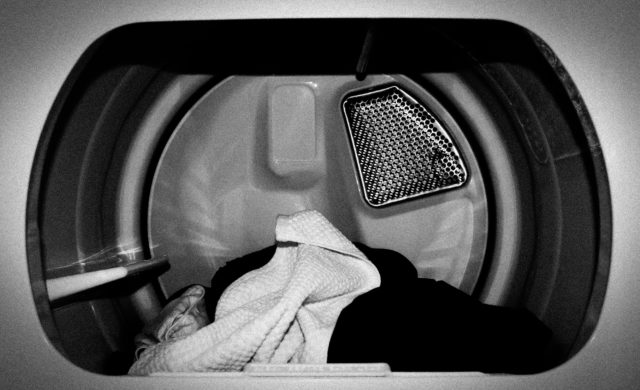
Reduce Plastic Sticking with Dryer Panel Coatings
DECC SOLVES PROBLEM OF PLASTIC STICKING TO DRYER PANELS
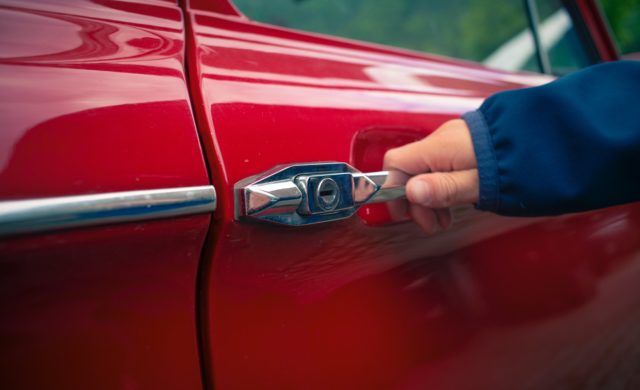
Coatings for a Quiet Ride
As cars have gotten quieter and quieter over the years, auto makers have...
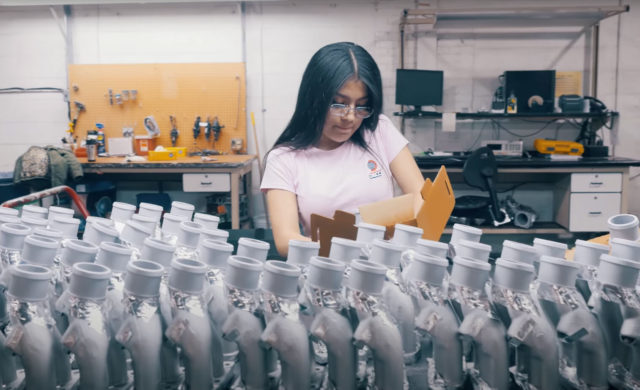
Dip Spin vs. Rack Spray – Why Not Both?
When it comes to the application of liquid-based functional coatings, there are two...