In today’s automotive manufacturing age, lightweighting is a popular, albeit almost necessary, approach for automobile manufacturers in an effort to improve the fuel efficiency of vehicles. With lightweighting, vehicle designers look to replace the heaviest vehicle components, such as steel panels, frames and assemblies, with lighter counterparts, such as aluminum or carbon fiber pieces.
Not only will this provide improved fuel efficiency, which all OEM’s are struggling with in light of the Obama administration’s minimum MPG requirements, lightweighting also helps improve the handling and performance of the car, something consumers have come to expect.
Also of note is that by swapping out heavy, costly components for materials like high-impact polymers and light metals, lightweighting makes traditional automotive construction more eco-friendly. In fact, the Wall Street Journal reports that every 10 pounds removed by lightweighting allows the car to produce 10-15 pounds less carbon dioxide emissions each year.
Where Lightweighting Falls Short
Unfortunately, lightweighting does present a series of problems. When converting some components to aluminum, the risk of dissimilar metals coming into contact and causing galvanic corrosion is increased…if not unavoidable.
Also, the polypropylene resins typically used to replace heavier materials are not scratch-resistant and plastic materials can be noisier than their original metal counterparts. Combined with the fact that there is less material to deaden this increased noise and another set of challenges arises.
This leaves the engineers responsible for lightweighting vulnerable: sure, they are making vehicles more eco-friendly and efficient, but is the performance and longevity of the automotive sacrificed in the process?
Fortunately, the functional coatings that DECC applies can solve at least some of these new challenges.
How Protective Coatings can Help
Today, high performance, functional coatings can help support lightweighting initiatives by stepping in to solve their deficiencies.
By adding functional coatings to certain components in lightweighted vehicles, manufacturers can enjoy their weight savings while also ensuring they perform at a level that is expected by consumers. This approach preserves the quality of lightweighted vehicles and cuts down on the unknowns that could impact the performance of the vehicles down the road.
As mentioned, because not everything can be converted to aluminum (or other lightweight alloys), there is the inherent risk of galvanic corrosion due to dissimilar metals coming in contact. Zinc-flake coating on components can prevent such corrosion. Not only can they prevent galvanic corrosion, zinc-flake coatings can provide up to 1500hrs or more of salt spray resistance. DECC applies zinc-flake coatings from Magni, Doerken and Atotech.
Because there are less heavy materials to absorb sound, every squeak and rattle is now amplified. Dry film lubricants on interfacing components can not only reduce or eliminate noise, but significantly increase the longevity of a component life-cycle. Whitford’s Xylan series are world class dry-film fluoropolymer coatings that have been solving these types of issues for decades. We also apply noise reduction coatings from Henkel and Dow.
The DECC Company: Your Source for Coating Solutions
While lightweighting is a necessary trend in the automotive industry, it can’t stand on its own. However, with the help of functional coatings, its shortcomings can be mitigated. This will allow both manufacturers and customers to take advantage of all the benefits of lightweighting without dealing with its obvious problems, like dissimilar metals meeting, corrosion, noise and a lack of durability.
By preserving lightweighted materials throughout the manufacturing process, coating solutions allow automotive companies to spend less time researching ways to make their materials work for the real world and more time developing strategies to produce eco-friendly, user-focused vehicles.
To learn more about all the challenges the functional coatings we apply can solve, contact us today.
Related Articles
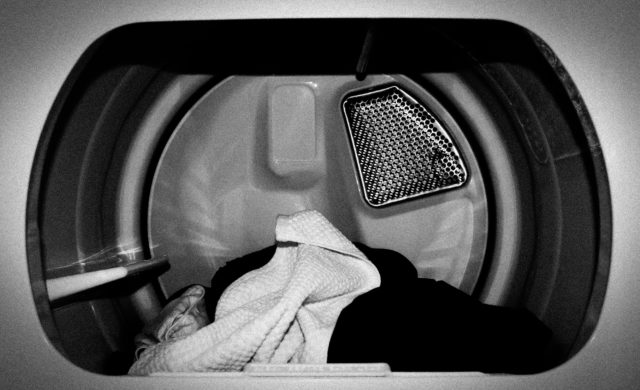
Reduce Plastic Sticking with Dryer Panel Coatings
DECC SOLVES PROBLEM OF PLASTIC STICKING TO DRYER PANELS
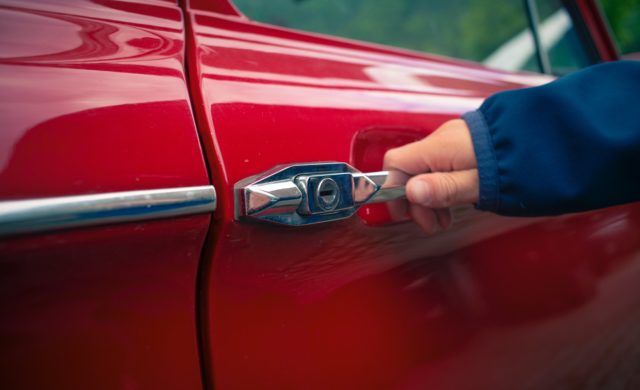
Coatings for a Quiet Ride
As cars have gotten quieter and quieter over the years, auto makers have...
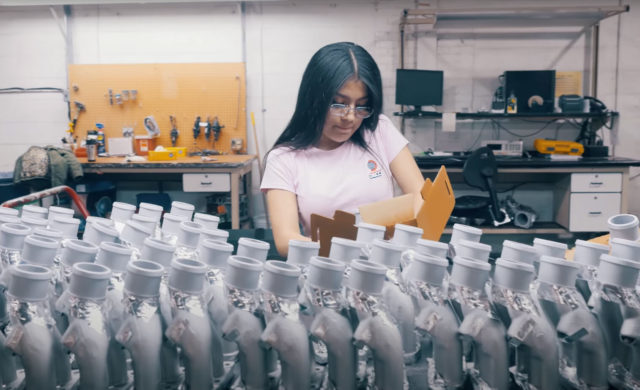
Dip Spin vs. Rack Spray – Why Not Both?
When it comes to the application of liquid-based functional coatings, there are two...