The DECC Company’s goal is to be the go-to resource for all of our customers’ functional coating application needs.
In that regard, we understand that we cannot be everything to every customer. As a result, we sometimes have to turn work away and refer it to a dip-spin competitor.
Why? Because for certain part geometries, it is the only processing method that is suited for that particular component. As much as we make the case that certain components should not be processed in a bulk method, there are many instances in which a part should not be processed via a rack-spray application.
Examples
Rack-spray coating requires what the name states – that every part is hung on a hook or inserted into a fixture. Because of this, there must be a place to “hold” the part.
With small fasteners, nuts, bolts and some stampings, this is not feasible. To hold a small fastener, it would most likely require being inserted into a cross bar of a fixture, ultimately completely masking one end and leaving it void of coating. And some small components do not have thru holes for a hook or, if they do, are too small.
In other instances, a thru hole (or trapped hole) could also be the contributing factor that inhibits a part from being rack-sprayed. For example, the part below has a threaded thru hole. The 8mm diameter is far too small and would prevent hardly any coating penetrating inside, ultimately leaving the entire center of the component void of coating. So even if there were quality issues or a surface finish requirement, this is not a component DECC could help with.

A bolt coated via dip-spin with a corrosion resistant coating
Tightly coiled springs are another problematic component that we cannot coat for two reasons. First, if a spring is too small, we would not be able to apply coating on the internal diameter due to the reasons above. Secondly, a spray method would not adequately build coating in between the coils and the part would not pass salt spray.
The last contributing factor that could prohibit a rack-spray application is price: if a part could be dip-spun and there are no finish requirements, we will usually provide a quote but also instruct our customer to seek out a dip-spin quote as well. Some parts could survive a dip-spin application, but would result in potential quality issues due to geometry. However, some customers only have a certain price point they can hit for outside processing and there are only so many things we can do that could reduce our price.
As mentioned, DECC aims to be a resource to our current and potential customers for all of their coating needs. If you have a question on whether or not something could or should be bulk coated, please contact us and we will point you in the right direction. Or if you are experiencing an issue with a current part this is being bulk coated and you think you may need a rack-spray application, please contact us as well.
Contact UsRelated Articles
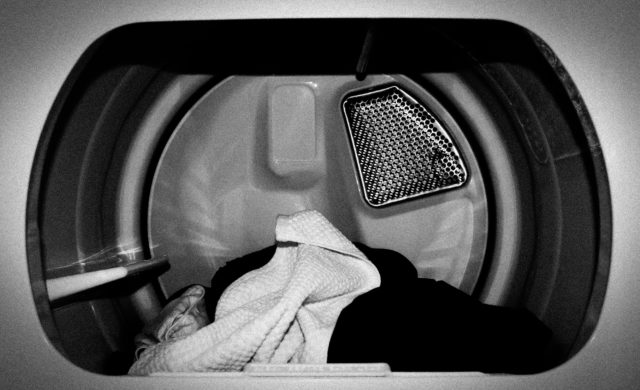
Reduce Plastic Sticking with Dryer Panel Coatings
DECC SOLVES PROBLEM OF PLASTIC STICKING TO DRYER PANELS
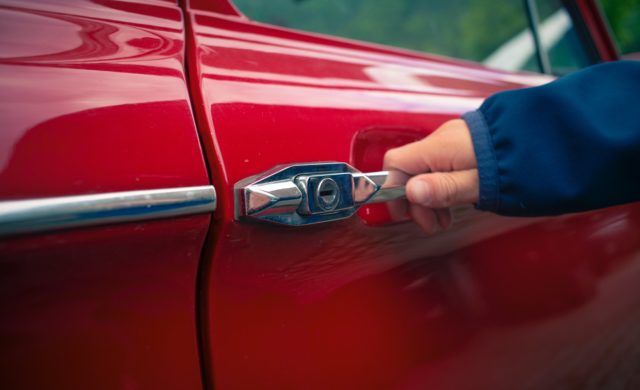
Coatings for a Quiet Ride
As cars have gotten quieter and quieter over the years, auto makers have...
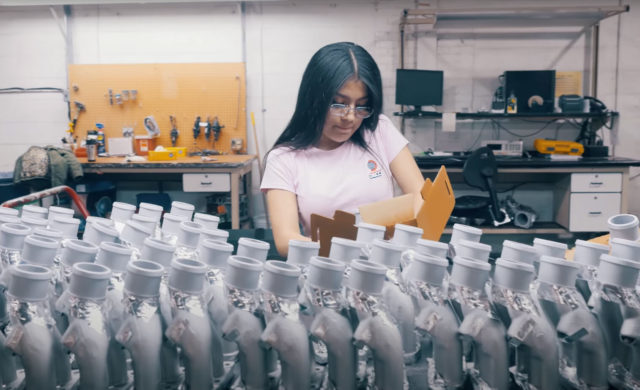
Dip Spin vs. Rack Spray – Why Not Both?
When it comes to the application of liquid-based functional coatings, there are two...