Minus components exposed to the elements that will always need some sort of corrosion protection, applying a functional coating to an automotive component is something most OEMs would prefer to avoid as it adds cost and extra processing steps.
However, as with the case with component performance/warranty issues, these parts were designed with the intention of not needing a functional coating as a solution or it would have been specified to begin with.
This is where the Preventative Care/Urgent care analogy comes into place.
In the case of Urgent Care or an ER, doctors are not afforded the luxury of providing input on preventative care. They have to deal with the situation at hand, regardless of how it got to that point. And sometimes actions leading up to needing the Urgent Care can limit what the nurses and doctors can do to fix the problem.
In many cases, when DECC is tasked to solve a performance issue for a customer, we are hampered by the literal design of the part in terms of what we can suggest as a solution. Ironically, the design is also what ultimately leads to the performance issue in the first place.
For example, a recent problem we solved for a customer pertained to the component and assembly design of the rearview mirrors having different components actuating and rubbing against each other.
On the surface, this may SEEM acceptable. However, some of the components were barrel plated without friction modifiers added to the sealer. And because it was barrel plated, it produced a rather rough finish, ultimately resulting in increased friction. Increased friction is a precursor to the emanation of noise. As a result, and especially when exposed to atmospheric conditions, these parts did not perform as intended and emitted a squeak when engaged.
When the customer approached us with the problem they were encountering, DECC had a solution in mind immediately. However, because of the preexisting plating on the component, we could not offer the solution we felt would be most beneficial to the customer because the cure temperature of the best coating solution would detrimentally break down the plating. And it would be exponentially harder to push thru two design changes as opposed to one, on top of a price increase that accompanies an added process.
Although the coating choice we offered was a “good” choice and solved their problems, it was not necessarily the “best” choice when assessing the performance requirements of the components to which it was applied.
If involved at the design stage (preventative care), a coating applicator can offer our knowledge and expertise to suggest a solution to a problem that may not be thought to be a problem to begin with. Involving a coating applicator as opposed to a manufacturer is also preferred as most applicators are not tied to the specific resin systems they produce, like a manufacturer, allowing greater diversity in potential solutions.
In many instances, the solutions DECC provides are added costs that aren’t necessarily essential to the design and function of a component because there MAY not be a performance issue. Then again, it is more costly to fix a problem than address it up front. However, it does us no good, nor our customers, if we offer an added cost that could be detrimental to either one of us securing new business.
The ultimate goal of being involved in the design stage of a component is about generating mutually beneficial relationships with our customers and providing education and resources to help them solve potential problems, even if we are not the solution…which is one of the foundational building blocks of our company and our culture.
Have a potential design issue or an existing part performance challenge? Contact us today to receive our input as to what the best solution would be for you and your customer. We may be the solution…we may not. But if we are not, we will help you find one with hopes of being able to assist on the next challenge.
Related Articles
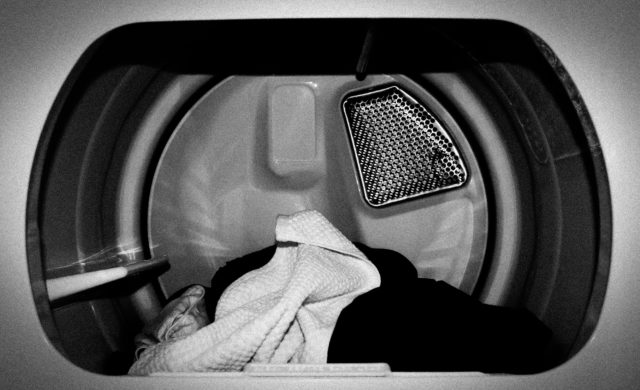
Reduce Plastic Sticking with Dryer Panel Coatings
DECC SOLVES PROBLEM OF PLASTIC STICKING TO DRYER PANELS
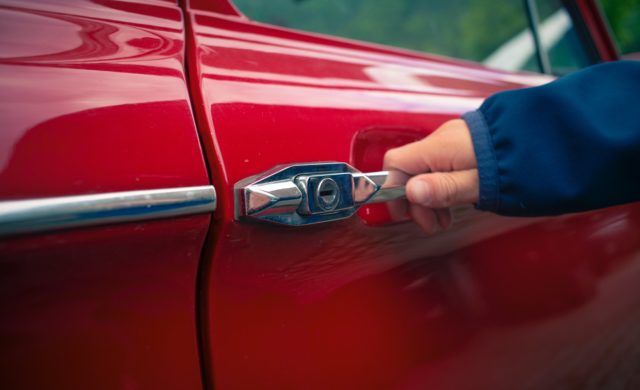
Coatings for a Quiet Ride
As cars have gotten quieter and quieter over the years, auto makers have...
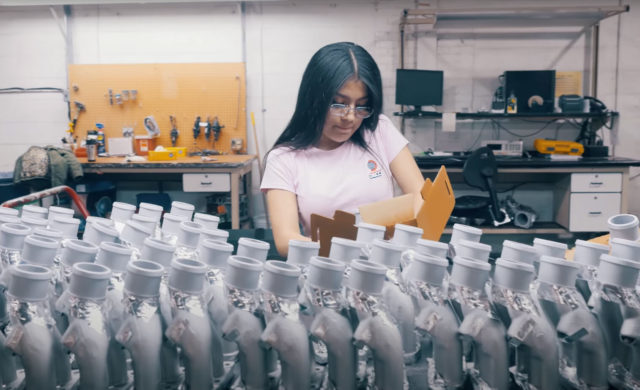
Dip Spin vs. Rack Spray – Why Not Both?
When it comes to the application of liquid-based functional coatings, there are two...