Ideally, today’s digital welding equipment can be fine-tuned to the point of producing almost zero spatter and weld engineers and technicians can lay a beautiful weld at the start of production with brand new equipment.
However, in a real world production setting, weld variables rarely stay tuned to a laboratory type setting. Weld fixtures become misaligned. Component tolerances vary over time. Weld equipment becomes worn. Weld variables change with every new trouble shooting attempt. Ultimately, these all contribute to the buildup of weld spatter.
There are multiple solutions to preventing mig weld spatter from building up and causing quality or productivity issues in your high volume welding environment.
Manually cleaning the spatter is the first, most obvious way. However, this method causes costly delays and disruptions in productivity due to cleaning weld fixtures with hammers, screwdrivers, air chisels or any other blunt force object operators can get their hands on. It also leads to the quick degradation of weld fixtures and equipment from the constant, albeit necessary, abuse.
Alternatively, an aerosol, spray-on temporary anti-spatter chemical may be a solution. Although initially functional, it does create a mess on the weld fixtures. It also requires the inventory of the anti-spatter product and the ongoing expense. Ultimately at every weld fixture PM, the oily mess needs to be washed off, along with any weld spatter that may have adhered due to the anti-spatter spray not being completely effective. In some cases, the spatter will even adhere to the buildup of anti-spatter spray.
The best overall solution is a permanent coating technology. This coating is sprayed on the fixtures and cured at a high temperature.
Once cured, this weld spatter resistant formula prevents any spatter from sticking. It eliminates the need for anti-spatter aerosol sprays and the constant scraping or chiseling of spatter off from weld fixtures.
To validate and showcase the performance characteristics of this coating, DECC performed a weld spatter test. We applied 100 welds to a vertical flat surface with a half uncoated, half spatter resistant coated surface plate 6” horizontally underneath the welds.

The test fixture with a side by side comparison of a half coated, half un-coated panel
When the coated and uncoated surfaces were compared, the coated surface had zero weld spatter adhering to it.
DECC regularly applies this coating to weld fixtures for numerous different customers. When spatter doesn’t stick to weld fixtures, productivity goes up and quality issues go down. Our customers are seeing:
- Reduced downtime from elimination of spatter removal
- Reduced damage to the weld fixture from concussive spatter removal
- Improved fit-up of welded components
- Reduced quality issues
- Reduced weld fixture consumables such as spatter guards, locating pins and nets pads
If you would like a sample coated for free so you can trial and see if this solution is a fit for your application, contact DECC today.
Related Articles
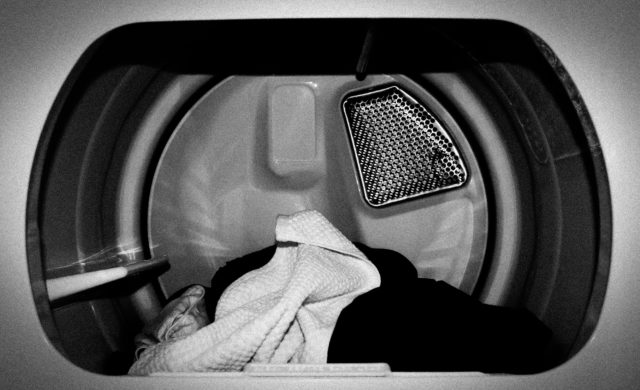
Reduce Plastic Sticking with Dryer Panel Coatings
DECC SOLVES PROBLEM OF PLASTIC STICKING TO DRYER PANELS
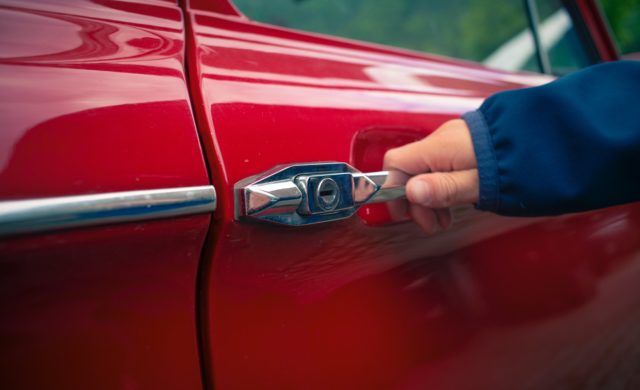
Coatings for a Quiet Ride
As cars have gotten quieter and quieter over the years, auto makers have...
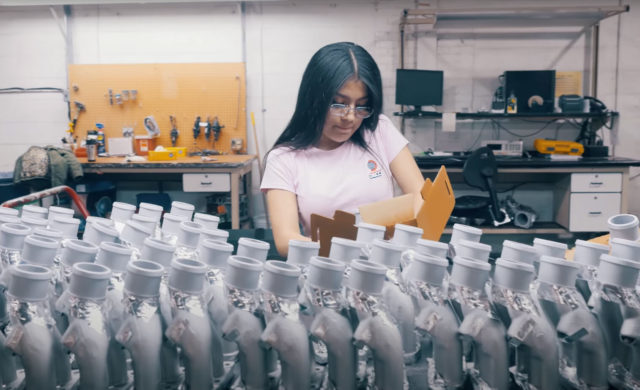
Dip Spin vs. Rack Spray – Why Not Both?
When it comes to the application of liquid-based functional coatings, there are two...