Galvanic Corrosion in the Automotive Industry
Galvanic corrosion challenges many industries, but none more than automobile manufacturers. Lightweighting of automobiles is an unavoidable necessity in the quest to improve fuel efficiency. As a result, galvanic corrosion is becoming a more prevalent issue.
In an effort to make automobiles lighter, different materials are being utilized throughout the vehicle, such as aluminum, composites and magnesium alloys, which all weigh much less than their steel or iron counterparts.
When these alternate dissimilar metals come in contact with each other it can then result in galvanic corrosion. The metal with the “lower positive electrode potential” suffers most of the corrosion. Metals like magnesium and aluminum are particularly in danger of this effect but are also in high demand for manufacturers.
Regardless of which option manufacturers choose, these lighter parts require extra protection to fight against galvanic corrosion. Two options for combating this problem are zinc-flake coatings and fluoropolymer coatings. These coating both work well and each has their own respective strengths.
Zinc-Flake Coatings
Zinc-flake coatings, such as those manufactured by Magni and Doerken, provide excellent corrosion resistance for parts to which they are applied, be it galvanic corrosion, atmospheric corrosion, chemical corrosion, etc.
These coatings are considered “sacrificial”: the zinc and/or aluminum in the coating oxidizes instead of the vehicle part to which it is applied. This means the coatings are essentially taking the stress and strain instead of vital car and truck parts. These coatings are commonly used on any parts that do not “flex,” at least not often, such as ridged brackets, fasteners, fuel tanks and mufflers…among others.
Zinc-flake coatings also function in excessive heat and cold and withstand acidic and basic chemicals. Lastly, these coatings are applied in extremely thin layers, meaning they add almost no additional weight to the components being coated.
Fluoropolymer Coatings
Fluoropolymers, such as Whitford’s Xylan series, are another excellent choice to combat galvanic corrosion. These coatings are considered a barrier coating that stops harmful substances from reaching the substrate.
In the case of galvanic corrosion, these coatings prevent dissimilar metals from actually “touching.” Fluoropolymers remain stable in the face of extreme temperatures, have superior chemical resistance and can also be utilized as a dry-film lubricant. In contrast to zinc-flake, fluoropolymers are flexible, which can help determine which coating to use.
Industry leaders in car manufacturing, as well as other industries, must protect their products from galvanic corrosion. In many cases, a functional liquid coating application can this process negatively impacting a component’s performance and longevity.
Since these coatings are applied in such thin film increments, they are particularly well suited to assist the efforts of lightweighting in the auto industry. Combining a functional zinc-flake or fluoropolymer coating application with a lightweight alloy can help manufacturers achieve the same, or sometimes better, part performance when compared to a component’s original, heavier counterpart.
If you are facing a corrosion issue, be it galvanic corrosion or any other type, contact us today.
Related Articles
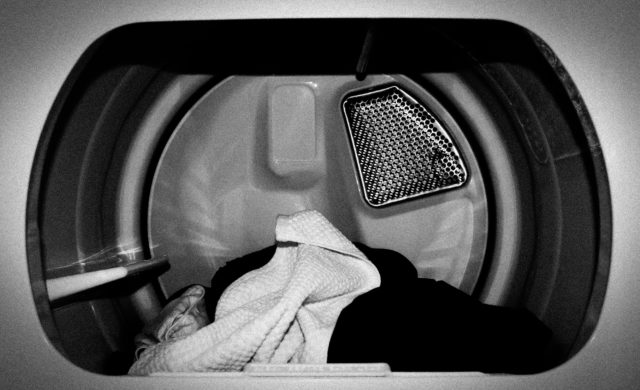
Reduce Plastic Sticking with Dryer Panel Coatings
DECC SOLVES PROBLEM OF PLASTIC STICKING TO DRYER PANELS
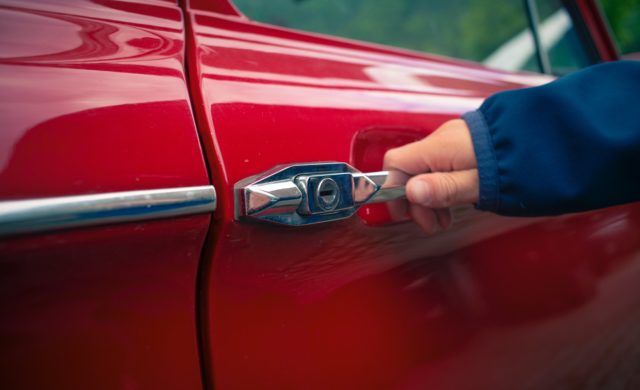
Coatings for a Quiet Ride
As cars have gotten quieter and quieter over the years, auto makers have...
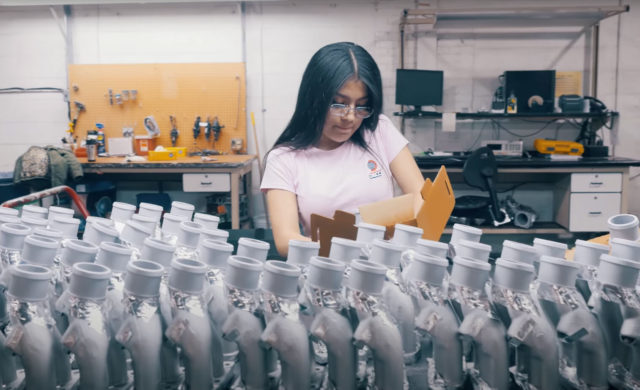
Dip Spin vs. Rack Spray – Why Not Both?
When it comes to the application of liquid-based functional coatings, there are two...