Over 80% of the requests we receive from current or potential customers deal with the application of coatings to combat corrosion, be it environmental, chemical, or temperature related.
However, of these requests, the majority are environmental. In these instances, most can be solved via a zinc-flake coating application. We will delve into ways to combat the other types of corrosion in another post.
WHAT ARE Zinc-Flake Coating Systems?
Zinc-flake coatings are sacrificial coatings which contain zinc and/or aluminum elements that oxidize sacrificially to ensure the substrate of to which they are applied remains corrosion free. These coating systems were designed for automotive and industrial parts that require greater protection than what standard paint and other coating systems can supply.
Zinc-flake coatings are used to protect non-flexing or rarely-flexing parts like brake rotors, drums and calipers; brake lines and hose clamps; fuel tanks and filler pipes; mufflers; the underside of hoods; clips, fasteners, springs and stampings; seat belt components and door lock components…and pretty much anything else that comes in contact with the elements and can survive a 450-degree curing cycle. These coatings can also prevent galvanic corrosion as a result of dissimilar metals coming in contact with each other. This is an extremely beneficial attribute in today’s age of light-weighting vehicles where aluminum components are more prevalent.
Advantages of Using Zinc-Flake Coating Systems
There are additional advantages to using zinc-flake coatings other than their primary function of providing excellent protection against corrosion.
Zinc-flake coatings are resistant to extreme temperature variations and can be modified with variable coefficient of friction characteristics for established torque requirements. They are not susceptible to warm-loosening torque and are resistant to both acidic and basic chemicals. Zinc-flake coatings also conduct electricity well if that is a required feature. Lastly, depending on the pre-treatment used, they do not introduce hydrogen embrittlement like standard plating does.
Zinc-Flake Coatings vs. Zinc Plating
Although we sometimes hear our customers refer to the zinc-flake coating we apply as “plating”, it is not. There are several key differences between a zinc-flake coating and zinc plating, as well as advantages and disadvantages to each surface treatment type.
As a general rule, zinc-flake coating lasts longer, is more resistant to corrosion, and is more predictable during the application process. All corrosive elements being equal, if a zinc plating lasts 250 hours before showing signs of protection failure, a zinc-flake coating can last 1,500 hours or more. Zinc-flake coating and zinc plating systems differ in both composition and application.
In terms of application, a zinc-flake coating process consists of spraying the coating on a part or dipping the component into the coating and spinning off the excess (DECC is an exclusively rack-spray coating facility). Zinc-flake coating is not an electrolytically applied coating, as is zinc plating. In essence, zinc plating is electro-galvanizing on a micro-scale. Using electro-deposition, zinc plating creates a chemical bond between the coating and the component, where zinc-flake coating produces a mechanical bond to the substrate.
As mentioned, another advantage of zinc-flake coatings is the fact that there is no hydrogen embrittlement associated with the application system, something the pre-treatment electro-cleaners and acid dips associated with zinc plating can induce. Hydrogen embrittlement is of particular importance with respect to maintaining the structural integrity of high-strength steel and was one of the contributing factors to the formulation of zinc-flake coatings in the 1970’s.
One advantage of zinc plating is that the plating can be applied in very thin layers. Also, it is an economical choice if the component does not require the lengthy corrosion protection that zinc-flake offers.
Types of Zinc-Flake Coatings
There are a few main players that specialize in the production of solvent-based zinc-flake coatings. In the United States, if a zinc-flake coating is called out on a part print, the majority of time either a Magni or Doerken coating system is an approved coating choice.
Magni Coatings has been around for over 40 years and their business is solely the production and distribution of zinc-flake coatings around the globe. One of the “gold standards” of the zinc-flake coating industry is Magni 565, which is an approved coating system on specifications of over 30 different OEM’s and Tier I suppliers in the automotive, military, agriculture, and commercial vehicle markets.
Doerken MKS has been producing zinc-flake coating systems since the 1980’s and is based out of Germany, where all of their coating products are manufactured. Known for their Delta-Protekt® base coats and varying Delta Seal® topcoats, they have recently introduced a new product – Delta Protekt® KL 120. This particular basecoat, when applied under even a black topcoat, can easily achieve over 2000 hours of salt spray protection with no appearance of white rust.
Atotech has been producing and distributing zinc-flake coating systems around the world for over two decades. Their presence is primarily outside of the United States, but they are known for their Zintec® basecoats and Techseal® topcoats.
DECC has been specializing in the rack-spray application of corrosion resistant coatings since their inception and can provide a quote or recommendation on which zinc-flake coating system we feel would be best for your current challenge.
Contact UsRelated Articles
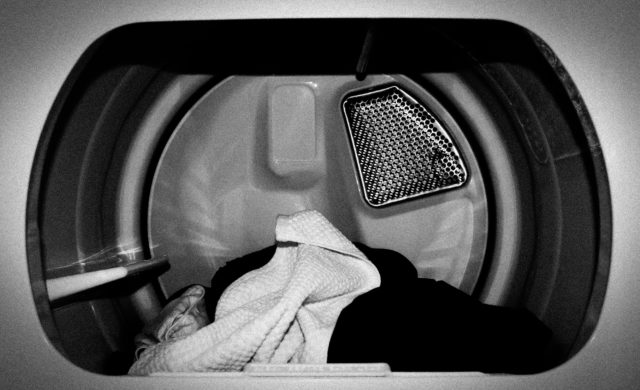
Reduce Plastic Sticking with Dryer Panel Coatings
DECC SOLVES PROBLEM OF PLASTIC STICKING TO DRYER PANELS
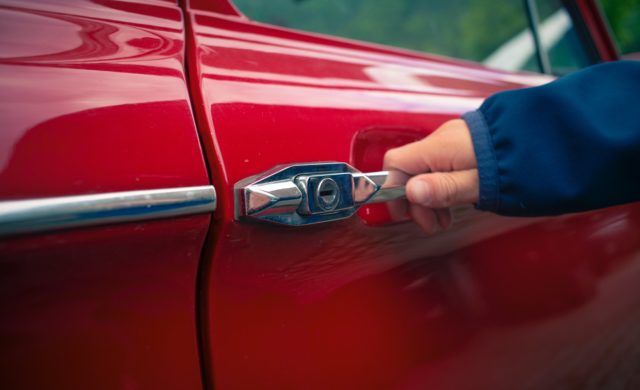
Coatings for a Quiet Ride
As cars have gotten quieter and quieter over the years, auto makers have...
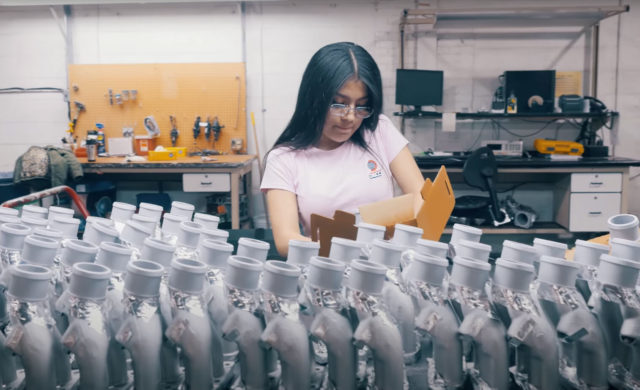
Dip Spin vs. Rack Spray – Why Not Both?
When it comes to the application of liquid-based functional coatings, there are two...